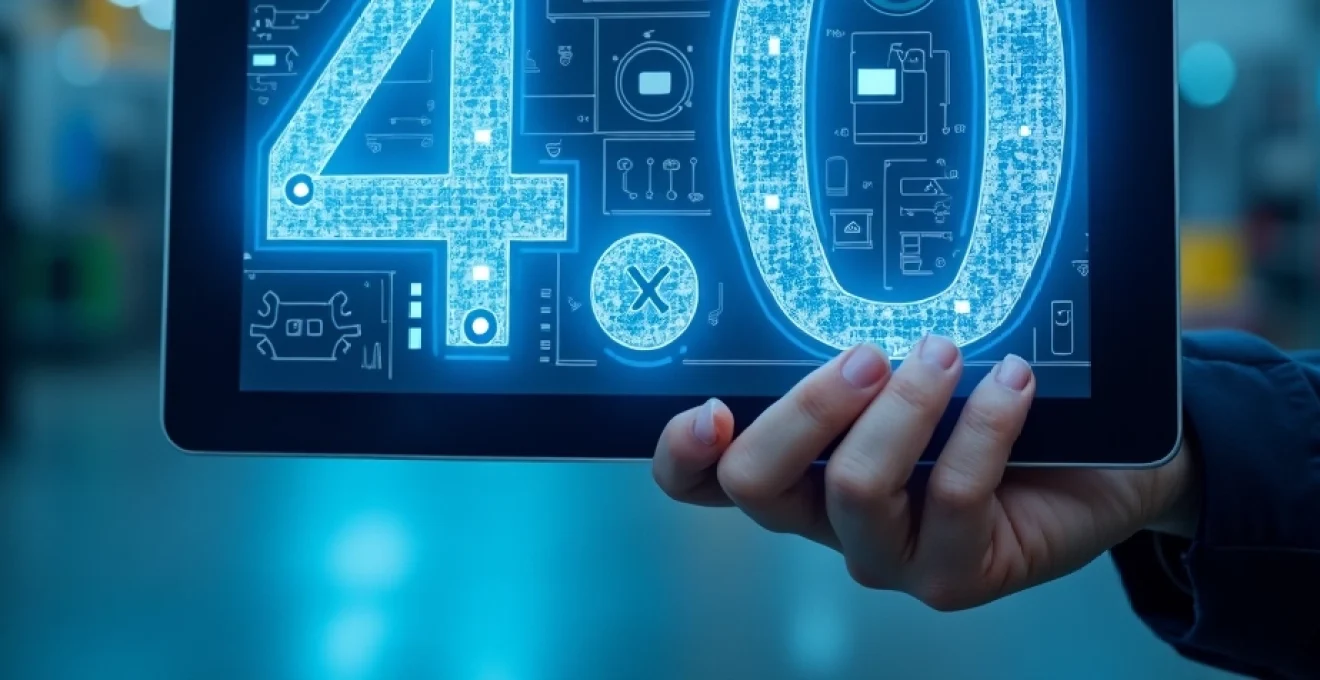
The industrial landscape is undergoing a profound transformation, driven by the advent of connected factories. These intelligent manufacturing environments leverage cutting-edge technologies to revolutionize production processes, enhance efficiency, and drive innovation. As businesses strive to remain competitive in an increasingly digital world, understanding the myriad benefits of connected factories has become crucial for industry leaders and decision-makers.
Connected factories represent the convergence of physical manufacturing systems with digital technologies, creating a seamless ecosystem where machines, products, and humans interact in real-time. This integration promises to unlock unprecedented levels of productivity, flexibility, and insight across the entire value chain. From optimizing operations to enabling predictive maintenance, the potential of connected factories to reshape modern industry is both vast and transformative.
Industry 4.0 and connected factory integration
Industry 4.0, often referred to as the Fourth Industrial Revolution, is the driving force behind the rise of connected factories. This paradigm shift is characterized by the fusion of advanced digital technologies with traditional manufacturing processes, creating smart, autonomous systems capable of self-optimization and adaptation. At the heart of Industry 4.0 lies the concept of connectivity, where every aspect of the production environment is interconnected and communicating constantly.
The integration of connected factory principles into existing industrial frameworks requires a holistic approach. It involves not just the implementation of new technologies, but also a fundamental rethinking of business models, workforce skills, and organizational structures. Companies that successfully navigate this integration can expect to see significant improvements in operational efficiency, product quality, and market responsiveness.
One of the key enablers of connected factories is the Industrial Internet of Things (IIoT). This network of smart devices and sensors forms the backbone of data collection and communication within the manufacturing environment. By leveraging IIoT, factories can achieve unprecedented levels of automation and real-time monitoring, leading to smarter decision-making and more agile production processes.
Real-time data analytics and operational intelligence
At the core of connected factories lies the power of real-time data analytics. By harnessing the vast amounts of data generated by sensors, machines, and processes, manufacturers can gain deep insights into their operations, enabling them to make informed decisions quickly and effectively. This operational intelligence is transforming how factories are managed, optimized, and improved on a continuous basis.
Real-time analytics in connected factories goes beyond simple monitoring. It involves complex algorithms and machine learning models that can predict outcomes, identify anomalies, and suggest optimizations. This level of intelligence allows for proactive management of production lines, reducing downtime and increasing overall equipment effectiveness (OEE).
Predictive maintenance with IoT sensors
One of the most impactful applications of real-time analytics in connected factories is predictive maintenance. By utilizing IoT sensors to monitor equipment health and performance, manufacturers can anticipate potential failures before they occur. This proactive approach to maintenance can dramatically reduce unplanned downtime, extend the lifespan of machinery, and optimize maintenance schedules.
Predictive maintenance algorithms analyze patterns in sensor data to detect early warning signs of equipment degradation. For example, vibration sensors on a motor can pick up subtle changes that indicate bearing wear, allowing maintenance teams to schedule repairs during planned downtimes rather than reacting to sudden breakdowns. This shift from reactive to predictive maintenance can result in significant cost savings and improved production reliability.
Machine learning for process optimization
Machine learning algorithms are playing an increasingly important role in connected factories, driving process optimization to new heights. These sophisticated models can analyze vast datasets to identify patterns and relationships that human operators might miss. By continuously learning from production data, machine learning systems can suggest optimizations that lead to improved quality, reduced waste, and increased efficiency.
For instance, in a complex chemical manufacturing process, machine learning algorithms can adjust production parameters in real-time based on input quality, environmental conditions, and desired output characteristics. This level of fine-tuning would be impossible for human operators to achieve consistently, highlighting the transformative potential of AI in connected factories.
Digital twin technology in manufacturing
Digital twin technology is revolutionizing how manufacturers design, test, and optimize their products and processes. A digital twin is a virtual replica of a physical product or process, created using real-time data from sensors and sophisticated simulation models. This technology allows engineers to experiment with different scenarios and optimizations in a risk-free virtual environment before implementing changes in the real world.
In connected factories, digital twins can be used to simulate entire production lines, enabling managers to test different configurations and identify bottlenecks without disrupting actual operations. This capability not only speeds up innovation cycles but also reduces the cost and risk associated with implementing new processes or products. As digital twin technology continues to evolve, it promises to become an indispensable tool for manufacturers seeking to stay ahead in a competitive global market.
Supply chain visibility and demand forecasting
Connected factories are not isolated entities; they are integral parts of larger supply chain networks. By extending the principles of connectivity and data sharing across the entire supply chain, manufacturers can achieve unprecedented levels of visibility and coordination. This enhanced visibility allows for more accurate demand forecasting, reduced inventory costs, and improved customer satisfaction.
Real-time data from connected factories can be integrated with supply chain management systems to provide a holistic view of the entire production and distribution process. This integration enables manufacturers to respond more quickly to changes in demand, optimize inventory levels, and identify potential disruptions before they impact production or delivery schedules.
RFID and blockchain in inventory management
Radio-Frequency Identification (RFID) technology and blockchain are two innovative technologies that are enhancing inventory management in connected factories. RFID tags allow for real-time tracking of materials and products throughout the supply chain, providing accurate, up-to-the-minute inventory data. When combined with blockchain technology, this creates a secure, immutable record of every transaction and movement within the supply chain.
The use of RFID and blockchain in inventory management not only improves accuracy and reduces the risk of theft or loss but also enables more sophisticated inventory optimization strategies. For example, manufacturers can implement dynamic reordering systems that automatically adjust based on real-time demand and supply chain conditions, ensuring optimal inventory levels at all times.
AI-driven demand prediction models
Artificial Intelligence (AI) is revolutionizing demand forecasting in connected factories. AI-driven prediction models can analyze vast amounts of data from multiple sources, including historical sales data, social media trends, economic indicators, and even weather patterns, to generate highly accurate demand forecasts. These sophisticated models can detect subtle patterns and correlations that traditional forecasting methods might miss, leading to more precise predictions.
By leveraging AI for demand prediction, manufacturers can optimize production schedules, reduce excess inventory, and improve customer service levels. For instance, a clothing manufacturer using AI-driven demand forecasting might be able to predict a surge in demand for certain styles or colors based on social media trends, allowing them to adjust production accordingly and capitalize on emerging market opportunities.
Just-in-Time manufacturing enablement
Connected factories are ideally suited to support Just-in-Time (JIT) manufacturing principles. JIT manufacturing aims to reduce inventory costs and improve efficiency by producing goods only when they are needed. The real-time data and advanced analytics capabilities of connected factories make it possible to synchronize production schedules with customer demand more precisely than ever before.
By integrating data from across the supply chain, connected factories can ensure that the right materials are available at the right time for production. This level of coordination reduces the need for large buffer inventories, minimizes waste, and improves cash flow. Moreover, the flexibility inherent in connected factory systems allows manufacturers to quickly adjust production in response to changes in demand or supply chain disruptions, making JIT manufacturing more resilient and adaptable.
Collaborative robot integration for flexibility
Collaborative robots, or cobots, are becoming increasingly common in connected factories, offering a new level of flexibility and efficiency in manufacturing processes. Unlike traditional industrial robots, cobots are designed to work alongside human workers safely, combining the precision and consistency of automation with the flexibility and problem-solving skills of human operators.
In a connected factory environment, cobots can be quickly reprogrammed and redeployed to different tasks as production needs change. This flexibility is particularly valuable in industries with high product variability or frequent changeovers. For example, an electronics manufacturer might use cobots for tasks like PCB assembly, where the robots can be quickly reconfigured to handle different board layouts or component types, allowing for efficient small-batch production.
Quality control and compliance automation
Quality control and regulatory compliance are critical concerns in manufacturing, and connected factories offer powerful tools to address these challenges. By leveraging advanced sensors, machine vision systems, and AI-powered analytics, manufacturers can implement more comprehensive and efficient quality control processes. These technologies enable 100% inspection of products, catching defects that might be missed by human inspectors and ensuring consistent quality standards.
Automation of compliance processes is another significant benefit of connected factories. By integrating regulatory requirements into the production system and automatically collecting and documenting compliance data, manufacturers can reduce the risk of non-compliance and streamline auditing processes. This not only improves regulatory outcomes but also reduces the administrative burden associated with compliance management.
Computer vision for defect detection
Computer vision technology is revolutionizing quality control in connected factories. Advanced camera systems coupled with AI algorithms can inspect products at high speeds, detecting even subtle defects that might be invisible to the human eye. These systems can analyze thousands of products per minute, providing 100% inspection coverage without slowing down production lines.
For example, in a pharmaceutical packaging line, computer vision systems can verify that each package contains the correct number of pills, check for damaged tablets, and ensure that labeling and expiry dates are correct. This level of inspection not only improves product quality but also enhances patient safety and regulatory compliance. The data collected by these systems can also be used to identify trends and root causes of defects, enabling continuous improvement of manufacturing processes.
Smart sensors for environmental monitoring
Environmental conditions can have a significant impact on product quality and process efficiency in many industries. Connected factories utilize networks of smart sensors to monitor and control environmental parameters such as temperature, humidity, air quality, and lighting. These sensors provide real-time data that can be used to maintain optimal conditions for production and storage.
In sensitive manufacturing environments, such as semiconductor fabrication or pharmaceutical production, even minor variations in environmental conditions can have serious consequences. Smart sensor networks in connected factories can detect deviations from ideal conditions and trigger immediate corrective actions. For instance, if humidity levels in a clean room start to rise, the system can automatically adjust HVAC settings to bring conditions back within specification, ensuring consistent product quality and regulatory compliance.
Automated regulatory reporting systems
Regulatory compliance is a complex and time-consuming aspect of manufacturing, particularly in highly regulated industries like pharmaceuticals, medical devices, and aerospace. Connected factories can significantly streamline compliance processes through automated regulatory reporting systems. These systems integrate with production data sources to automatically collect, analyze, and compile the information required for regulatory submissions.
Automated reporting systems not only reduce the administrative burden of compliance but also improve the accuracy and timeliness of regulatory submissions. By eliminating manual data entry and processing, these systems reduce the risk of errors and ensure that all required data is included in reports. Moreover, they can provide real-time visibility into compliance status, allowing manufacturers to proactively address any potential issues before they become regulatory violations.
Energy efficiency and sustainable manufacturing
Sustainability is becoming an increasingly important focus for manufacturers worldwide, driven by both regulatory pressures and consumer demand for environmentally responsible products. Connected factories offer powerful tools for improving energy efficiency and implementing sustainable manufacturing practices. By providing detailed, real-time data on energy consumption and resource usage, these systems enable manufacturers to identify inefficiencies and optimize their operations for sustainability.
Advanced analytics and machine learning algorithms can analyze energy usage patterns across the factory, identifying opportunities for reduction and suggesting optimizations. For example, an AI system might identify that certain machines are being left idle during shift changes, wasting energy. By automatically powering down these machines during downtime, significant energy savings can be achieved without impacting productivity.
Smart grid integration for power management
Connected factories can be integrated with smart grid systems to optimize power consumption and take advantage of variable energy pricing. By connecting factory energy management systems to the smart grid, manufacturers can adjust their energy usage based on real-time pricing signals, shifting energy-intensive processes to times when electricity is cheaper or more abundant.
This integration also enables factories to participate in demand response programs, where they can reduce their power consumption during peak demand periods in exchange for financial incentives. For example, a connected factory might automatically reduce its cooling load during a hot summer afternoon when the grid is under stress, helping to prevent brownouts and earning credits from the utility company.
Waste reduction through connected systems
Waste reduction is a key aspect of sustainable manufacturing, and connected factories provide powerful tools for minimizing waste throughout the production process. By providing detailed visibility into material usage and production processes, these systems can help identify sources of waste and inefficiency. Machine learning algorithms can analyze production data to optimize processes, reducing scrap and improving yield.
For instance, in a plastic injection molding process, connected systems might analyze data from sensors monitoring temperature, pressure, and material flow to identify the optimal parameters for minimizing flash and other defects. By continuously adjusting these parameters based on real-time data, the system can significantly reduce material waste while improving product quality.
Circular economy facilitation with IoT
The Internet of Things (IoT) technology underpinning connected factories is also enabling new approaches to the circular economy. By embedding sensors and connectivity into products, manufacturers can track their lifecycle, monitor usage patterns, and facilitate refurbishment or recycling at end-of-life. This approach not only reduces waste but also opens up new business models based on product-as-a-service or performance-based contracts.
For example, a manufacturer of industrial equipment might use IoT sensors to monitor the performance and condition of their products in the field. This data can be used to schedule predictive maintenance, extending the product's lifespan. When the product reaches the end of its useful life, the manufacturer can use the collected data to optimize the refurbishment process or ensure efficient recycling of components. This closed-loop approach maximizes resource efficiency and minimizes environmental impact.
Cybersecurity and data protection in connected factories
As factories become more connected and reliant on digital systems, cybersecurity emerges as a critical concern. The increased connectivity and data flow in smart factories create new vulnerabilities that malicious actors could potentially exploit. Protecting sensitive manufacturing data, intellectual property, and operational technology (OT) systems from cyber threats is paramount for maintaining the integrity and competitiveness of connected factories.
Implementing robust cybersecurity measures in connected factories requires a multi-layered approach. This includes securing network infrastructure, implementing strong access controls and authentication mechanisms, encrypting sensitive data, and regularly updating and patching systems. Additionally, manufacturers must develop comprehensive incident response plans to quickly detect and mitigate any security breaches.
Employee training is also crucial in maintaining cybersecurity in connected factories. As human error remains one of the most significant cybersecurity risks, ensuring that all staff members understand basic security principles and can recognize potential threats is essential. Regular security audits and penetration testing can help identify vulnerabilities before they can be exploited by attackers.
The convergence of IT and OT systems in connected factories presents unique cybersecurity challenges. Traditional IT security measures may not always be suitable for OT environments, where system availability and safety are paramount. Manufacturers must develop specialized security strategies that protect against cyber threats without compromising the real-time performance and reliability requirements of industrial control systems.
As connected factories continue to evolve, so too must their cybersecurity measures. The adoption of technologies like AI and machine learning for threat detection and response, along with the implementation of zero-trust architectures, will be crucial in staying ahead of emerging cyber threats. By prioritizing cybersecurity and data protection, manufacturers can ensure that the benefits of connected factories are realized without compromising the security and integrity of their operations.